ULMA Packaging installs several automated packaging lines in Coral LLC, one of the largest meat producers in Russia
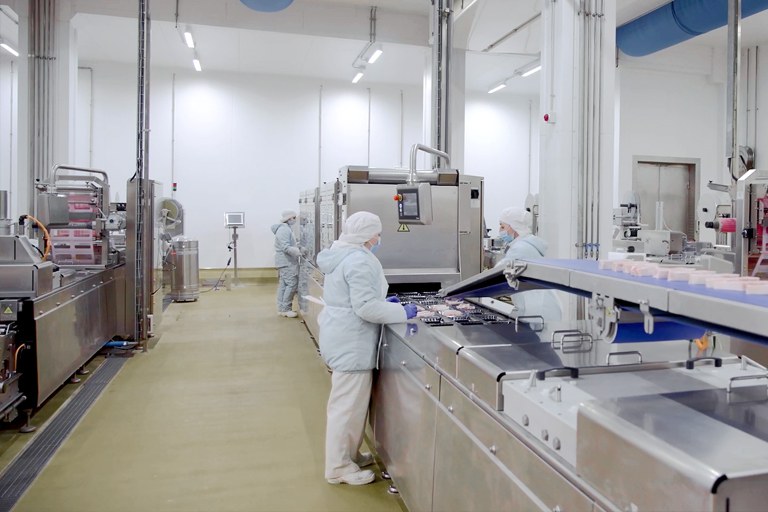
Coral LLC, a newly-created Russian company, is one of the country's largest pork producers. In 2012, the firm started implementing a pork production investment programme that would include a plant for processing the pork, as part of the livestock complex that included the meat processing plant, with a production capacity of 450 thousand animals per year. This project is part of a new major agro-industrial complex, with total investment amounting to 320 million euros and resulting in the creation of over 1,500 jobs; a huge-scale project that required a supplier who was capable of offering a comprehensive, integrated packaging solution.
Against this backdrop, ULMA Packaging was the company that was chosen to supply the packaging and packing equipment because it offers the most advanced machinery of its kind and meets all of the food production safety requirements, bearing in mind that Coral LLC has an innovative control system to ensure the quality of the meat cuts. Coral LLC's production departments have been equipped with high-tech equipment that complies with the production safety standards in Russian legislation and the international standards. Monitoring the technical and technological operations during each stage of production and the continuous improvement of the company's processes will allow Coral LLC to produce high-quality natural meat products with a long shelf life; excellent tasting food at an attractive price.
ULMA Packaging's team offered a comprehensive advisory and consulting service, using its experience as experts in meat packaging products to propose the most suitable solution design for the processing and packaging lines for their case-ready products. Throughout the process, it offered all of its knowledge and experience to provide the customer with technical advice to obtain a complete solution that was tailored to its needs. The biggest challenge overcome by ULMA Packaging in this unique project was to create a more compact layout of all of the equipment for the preparation and packaging of the product, optimising the production area with the most suitable plant layout. We also provided a comprehensive solution that featured everything from Flow-Vac® packaging to thermoforming, including cutting, preparation and packing equipment and industrial weighing, labelling and metal detection at the exit.
Case-ready thermoforming area
The thermoformer packaging lines supplied by ULMA Packaging allow the cost of packaging material to be reduced, resulting in a better-priced final product with no loss of quality. The high standards of hygiene and automation ensure a long shelf life for the entire product line. And there is no doubt that the packaging equipment supplied by ULMA Packaging plays a vital role in achieving this result. The minimal residual oxygen content and high vacuum level achieved thanks to the carefully designed specifications of the equipment, increase the shelf life without using preservatives that reduce the quality of the product. The five pork thermoforming packaging lines are used for:
- Minced meat line.
- Industrial cutting line.
- Line for marinated meat in ovenable film.
- Filleting line.
- Line for small pieces e.g. for goulashes, barbecues, etc.
Cardboard box forming area
The cardboard box forming area with case erectors was placed on the second floor, to significantly reduce the space occupied in the main department. This required a complex system of conveyors to deliver the cardboard boxes to the first floor. The chosen solution consisted of the automatic forming of the boxes and their automatic distribution to each line.
In a project of this kind, automating the different processes is essential to ensure the production and quality of the final product. So, ULMA Packaging automated the product preparation lines, the lines for packaging, product control and labelling, as well as the automatic case packing.
Industrial cutting
For packaging in the industrial cutting area, ULMA Packaging supplied several automatic Flow-Vac® packaging lines that collect the product from the butchering lines and automatically proceed to a packaging system that optimises the material, a solution that is perfectly suited to the characteristics of the product and its subsequent sale. Flow-Vac® technology provides the best in-line packaging solution for vacuum-packed industrial cuts, minimising any handling of the product, reducing the level of leakages and reprocessing, which has made it the preferred solution of most leading meat producers. It is also popular because of its sustainability, as the amount of film used in the packaging is significantly reduced.
Plastic crate washing and logistics
In the final phase of the project, we presented a solution to implement the entire logistical process for the plastic crates. The design of the solution was implemented with a used crate conveyor system to the washing machine on the top floor, after which they were conveyed to the butchering area.
ULMA, close contact with the customer
In terms of the commissioning of the lines, proper planning of the logistics system and organisation of the work enabled us to provide prompt technical training to the required number of operators and for industrial production to begin within the terms specified by the customer. Throughout this project, ULMA Packaging has demonstrated its service capabilities, providing the customer with a team of multidisciplinary experts during the analysis, advisory, installation and commissioning phases of the project and in the provision of preventive maintenance, local spare parts, etc. Our close contact with the customer, the ongoing on-site presence of ULMA Packaging's experts and our rapid response to the project's various requests and requirements were key factors in this highly complex, huge-scale project.
ULMA Packaging has a strong focus on customer relations both during the implementation of the project and after it has been launched, with expert technical support that guarantees the success of the project and serves as a benchmark for any future large-scale installations.