Hygiene thermoforming machines
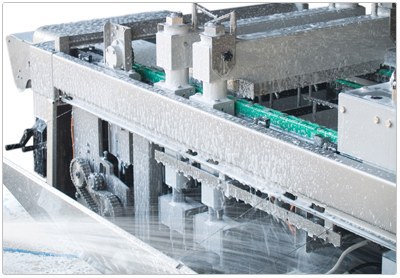
The most demanding sectors require washing and deep hygienic
cleaning of all the elements in contact with the product which is
susceptible to contamination. These high levels of equipment hygiene,
calls for specific designs capable of supporting corrosive detergents,
high-pressure water systems and disinfection procedures.
The new
range of thermoforming machines from ULMA is designed to allow cleaning at the workplace. The attention to detail is highlighted by the
following benefits:
ACCESSIBILITY
Areas prone to accumulation of deposits and residue should be eliminated and allow easy access to cleaning.
Generally
the machines must have easy access for inspection, maintenance,
cleaning and disinfection procedures. The detailed hygienic design
should not be limited to the visible perimeter of the machine, but
also integrated with the working parts on the inside of the machine.
SELF-DRAINING SURFACES
All
surfaces should promote effective drainage of water, detergents and
disinfectants used during the cleaning and disinfection procedures.
Likewise the interior of the machine is designed in such a way that both solid residue and the liquids do not accumulate.
CONTACT BETWEEN PARTS
The
areas where residue could accumulate, promoting the proliferation of
bacteria, must be eliminated by adopting advanced hygienic engineering
designs. This is made possible by means of watertight, continuous
welding runs or alternatively avoiding acute angles, allowing effective
cleaning between working parts.
RESISTANCE TO CORROSION
Only
high quality stainless steel and other food-grade materials, suitable
for the food industry are selected, providing a completely corrosion
resistant construction.
DEGREE OF IP PROTECTION
The
most critical electrical and pneumatic areas are protected by
watertight compartments, providing a protection rating of IP 67 or
even IP 69 where the areas require more intense cleaning.
In
extreme cases and at the client's request, the main electrical
compartment can be separated from the machine in a specially protected
area.
The new range of thermoforming machines TFS include 4
different models, tailored to suit the customer’s production and
packing needs.
All the models of the TFS range have been
designed with the sanitation concept in mind and therefore comply with
the new market requirements regarding strict cleaning and hygiene
procedures in the packing areas.
The TFS 700, the model with
the highest specifications of this new range, has been developed with a
flexible chassis that allows using film widths from 320 to 720 mm wide.
The machine is capable of forming packages 210mm deep and advances of
up to 1,100 mm
This allows high production levels and demanding package formats when needed.
Fit
for purpose, the machine has an exceptionally robust chassis, different
lifting systems, with two or three columns and pneumatic or motorized
activators. All machine elements are controlled by an industrial PC,
with the possibility of obtaining data and production statistics.
The
necessary interfaces has been developed for integration in automatic
packing lines that incorporate elements such as artificial vision for
detecting products, loading robots, container inspection, contents
inspection, closure safety, unloading robots for latter boxing and
palletizing of the containers.
The complete TFS range - 200,
300, 500 and 700, keep and in many cases have improved the
characteristics that have made the ULMA thermoforming machines so
popular in European markets:
- Easy to use
- Simple and friendly interface
- Low level of maintenance
- Flexibility
- Ergonomics
- Ease in format changes
The new range of TFS thermoforming machines has been presented
in the Trade Fairs: BTA-HISPACK that was celebrated in Barcelona from
11 to 15 May and in Tecnocarne celebrated in Verona from 15 to 21 May.
During
the BTA-HISPACK Trade Fair, the new range of thermoforming machines
attracted a lot interest and the visitors noted that ULMA’s
thermoforming range is well positioned in the market. Together with
this new release, the following product applications and were presented:
- Integrate solutions for automatic packing lines including a new line of thermosealing machines with automatic tray de-stackers, automatic product dosing, metal detectors, etc.
- Dairy product packing, desserts and sub-products including product dosing and container decoration.
- Automated product loading for different equipment utilising robots.
- Automatic boxing and palletizing units.